
QUELLES MACHINES ET QUELS MOULES SONT UTILISÉS DANS LE ROTOMOULAGE?
Introduction
Le rotomoulage est une technique de fabrication qui permet de créer des pièces en plastique creuses de toutes formes et de tailles très variées. Ces objets aux contours complexes, à la surface lisse ou texturée, sont issus d'un processus ingénieux. Indispensables, les machines sont de véritables chefs d'orchestre durant le processus : elles tournent et chauffent le moule, assurant une répartition uniforme du matériau plastique. Les moules quant à eux donnent forme à vos idées en accueillant le plastique en fusion et en créant les contours souhaités. La conception minutieuse de chaque moule est essentielle pour obtenir un résultat parfait. Découvrez ce qu’il faut savoir sur ces éléments incontournables du rotomoulage.​
Plusieurs types de machines pour le rotomoulage
La première apparition du rotomoulage remonte à plus de 150 ans, quand le procédé est imaginé pour créer des munitions d’artillerie au milieu du XIXe siècle. C’est véritablement à partir des années 1930 que les précurseurs des machines actuelles commencent à être utilisés.
Entre trois et quatre parties principales sont retrouvées sur ces appareils :
​
​
​1. Un four :
c’est dans cette partie que le moule reçoit la chaleur nécessaire pour faire fondre le plastique. Il peut fonctionner au gaz, à l'électricité ou avec d'autres sources d'énergie. La température du four est variable selon le matériau utilisé, mais elle est généralement d'environ 260 à 370 degrés Celsius ou 500 à 700 degrés Fahrenheit ;


2. Une unité de rotation :
cette partie de la machine fait tourner le moule sur deux axes perpendiculaires. La rotation bi-axiale permet de répartir uniformément le matériau plastique fondu à l'intérieur du moule. La vitesse de rotation et les angles sont ajustables selon la forme et la taille de la pièce à produire ;​
3. Une zone pour le refroidissement :
cette partie accueille le moule pour être refroidi progressivement à l'air. Le refroidissement est indispensable, car il permet au plastique de se solidifier et de prendre ainsi la forme voulue ;
4. Une zone de déchargement et de chargement :
après le refroidissement, le moule est ouvert afin de retirer la pièce en plastique formée. Le moule est ensuite rechargé avec du plastique pour recommencer le cycle de chauffage.

Les machines à clapet
Ces appareils regroupent dans un seul poste de travail les unités de chauffage, de refroidissement et de déchargement et de chargement. Les machines à clapet sont constituées d’un seul bras rotatif. Leur cycle de production est relativement rapide et leur installation demande peu d’espace. Leur coût d'investissement est aussi moins important par rapport aux machines plus complexes. Les machines à clapet conviennent davantage pour la production de pièces de taille moyenne à grande, comme les réservoirs de carburant par exemple, ou les bacs de stockage et les équipements de jardinage. Elles sont moins adaptées pour les très grandes pièces et leur cycle de production continu n’est pas aussi rapide que celui des machines à carrousel.
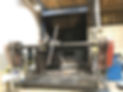
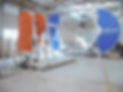
Les machines navettes
Ce type de machine fonctionne grâce au déplacement des moules entre les différentes unités, notamment entre le poste de chauffage, celui de refroidissement et de déchargement/chargement. Les machines navettes utilisent un bras mobile pour transférer les moules d’une partie à l'autre. Leur grande flexibilité dans les étapes de production leur permet de travailler avec plusieurs moules de dimensions et de formes variées de manière simultanée. Elles ont une importante faculté d’adaptation avec de larges contraintes de production. Les machines navettes sont ainsi des appareils parfaits pour la fabrication de pièces de grandes dimensions comme les réservoirs d'eau et les bateaux par exemple. Le coût initial de ces machines est néanmoins élevé et l’encombrement nécessaire à leur installation est souvent plus important.
Les machines basculantes ou machines Rock and Roll
Les machines Rock and Roll combinent une rotation axiale et un mouvement de bascule pour répartir de manière uniforme le matériau plastique. Elles intègrent un bras principal tournant le moule dans un axe longitudinal ainsi qu’une plateforme qui bascule d'avant en arrière. La répartition du plastique est ainsi optimale, même pour les pièces aux formes les plus complexes. Les machines basculantes sont ainsi idéales pour la fabrication d’objets longs et étroits. Elles sont habituellement utilisées pour concevoir des canoës, des réservoirs allongés et des équipements de sport nautique. Ce type de machine est moins adapté pour les grandes productions.
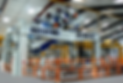
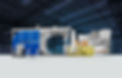
Les machines à carrousel
Les machines à carrousel ont une structure rotative avec plusieurs bras, généralement au nombre de trois ou quatre. Chaque bras peut porter un ou plusieurs moules. Les bras tournent autour d'un axe central, passant par les différentes unités au cours d’un cycle continu. Les caractéristiques de ce type de machine lui permettent d’assurer une productivité élevée. Les spécialistes de la plasturgie qui utilisent une machine à carrousel sont très efficaces pour la production de grandes séries de pièces, en raison du temps d'arrêt réduit de l’appareil entre les cycles. Les machines à carrousel sont déconseillées lorsque la fabrication nécessite un changement fréquent de moules.
Que savoir sur les moules utilisés dans le rotomoulage ?
Dans le rotomoulage, l’utilisation de la machine adéquate est indispensable. Au même titre que ces appareils, les moules ont aussi un rôle crucial. Ils déterminent la forme finale et les détails des pièces souhaitées. La qualité du moule influence directement celle de la pièce rotomoulée. Ils sont ainsi conçus avec précision pour garantir des dimensions exactes et des finitions de haute qualité afin que les pièces respectent les spécifications techniques requises. La rigueur et le savoir-faire des moulistes sont donc primordiaux.
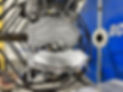
Fabrication sur mesure de moules en fer ou en acier
Plusieurs matériaux sont susceptibles d’être utilisés pour la conception des moules, les plus fréquents étant notamment l’aluminium et l’acier. Un moule en aluminium a l’avantage d’être plus léger. Les atouts de ce type de moule reposent aussi sur sa capacité accrue à transmettre la chaleur et d’être plus facile à travailler. Les spécialistes de plasturgie ont recours aux moules en aluminium lors de la production de pièces complexes présentant des détails fins. Les moules en acier, sont de leur côté, plus robustes et durables. Ils sont néanmoins plus lourds et plus difficiles à travailler. Les moules fabriqués en acier sont davantage employés pour la production de pièces de grandes dimensions ou lorsque le volume de production est très élevé.
Des types variés de moules pour le rotomoulage
En acier ou en aluminium, les moules sont travaillés selon différentes méthodes et technologies. Plusieurs critères sont considérés lors du choix du moule à utiliser avant la fabrication des pièces, notamment le coût, la durabilité ou le niveau de précision souhaitée.
Les moules en aluminium coulé
Ils sont fabriqués en versant de l'aluminium fondu dans une forme ou un modèle. Une fois refroidi et solidifié, le moule est usiné pour les détails finaux. Ce type de moule est moins coûteux à fabriquer par rapport à ses analogues. Il est donc plus utilisé pour les productions de pièces en plastique en petite ou moyenne série. Les moules en aluminium coulé ont aussi l’avantage de permettre l’intégration de détails complexes directement lors du processus de coulée, même s’ils sont moins précis par rapport aux moules réalisés grâce à un procédé numérique.
Les moules en aluminium usiné par machine à commande numérique ou CNC
L’usinage CNC implique une fabrication à partir d'un bloc d'aluminium massif grâce à une sculpture du moule à l’aide de machines à commande numérique. Cette technique offre une précision exceptionnelle, lui assurant d’être parfaite pour la conception de pièces plastiques avec des tolérances strictes et une grande finesse des détails. Le coût d’un moule usiné par CNC est plus élevé par rapport aux autres types de moule.
​
Les moules en plaques d'aluminium ou d’acier
Ce type de moule nécessite l’assemblage de plusieurs plaques. Les moules sont en effet fabriqués en découpant et en assemblant des plaques de métal, souvent soudées ou réunies à l’aide de boulons pour former le moule final. Cette technique est la plus abordable, par rapport aux moules usinés ou coulés. Elle est donc particulièrement recommandée lors de productions de pièces plastiques en petite série ou pour les prototypes.
Conclusion
Les machines et les moules pour le rotomoulage vous ouvrent les portes d'un univers aux nombreuses facettes. Les technologies de pointe actuelles en plasturgie vous permettent de fabriquer des pièces plastiques aux formes complexes et sur mesure. Les moules de haute précision garantissent des produits finis de qualité supérieure, adaptés à des applications variées. Les machines de rotomoulage modernes, avec leurs capacités de chauffage et de rotation avancées, permettent une production efficace et rentable, même pour les petites et moyennes séries. Avec le rotomoulage, donnez vie à vos idées les plus audacieuses.