
All you need to know about rotomolding
Rotomolding (sometimes referred to as rotomoulding or rotational molding) is a plastic casting technique that uses heat and rotational force to form hollow objects. This versatile technology can be used to make a wide variety of products, including vessels and tanks of nearly any size or shape, food- and medical-grade containers, outdoor furniture, watercraft and children’s toys.
The process involves heating plastic powder in a mold until it melts and takes the shape of the mold and is then cooled. The mold is rotated during the entire heating and cooling process to evenly distribute the wall thickness of the part.
Rotoplast offers several service options. Our integrated service can help develop your new product from the ground up, including computer-aided design (CAD), mold tooling, parts creation, assembly and trimming. If you already have a production line, ask us about our mold and jig manufacturing service. For more complex projects or one-of-a-kind ideas, our custom production service meets you wherever you are in your process.
Which material do we use?
Almost all rotomolded products are made with some form of polyethylene (PE), a versatile polymer, ground to a fine powder. The recipe varies according to the product’s end-use requirements. Rotoplast typically uses the following types of resin:
L'équipe de Rotoplast peut vous conseiller sur les matériaux adaptés à votre projet.
The Mold
Molds are typically made of aluminum alloy or steel through a CNC machining and/or casting process. Depending on the nature of the part to be created, we will select the right process for your needs.

The rotomolding machine
Une machine de rotomoulage typique se compose de trois éléments principaux :
Rotoplast uses seven computerized ovens with large dimensional capacity. Their uniform heat distribution and high-velocity air circulation ensure products meet the highest quality standards.
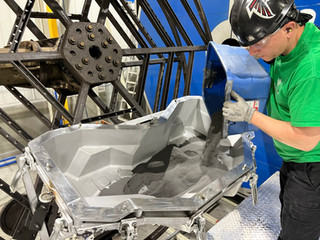
The Process
The rotomolding process can involve six phases:
-
Preparation. If required, supplementary components like metal fittings or decorative decals can be placed in the mold to embed with the molded part.
-
Loading. Sometimes called the “charging” phase, this is when the powder is measured according to product specifications and poured into the mold. The mold is clamped shut and conveyed into the oven.
-
Heating. The mold rotates at slow RPM on its spider, and powder will cascade inside the cavity until the mold reach the melting point of the resin and will towards the inner walls of the mold. The rotation is biaxial, meaning the object rotates in two different directions to ensure an even distribution and the thickness of the walls is a function of the amount of material used.
-
Cooling. The mold is moved into the cooling chamber, where the parts are exposed to forced air or water. The rotation continues during this phase of the process.
-
Discharging. Once the rotation stops — and only after the cooling process is completed — the cooled part is removed from the mold, or demolded.
-
Post-processing. This phase could include deburring, trimming, drilling and finishing or we can do CNC machining by a 7 axis robot. We also offer polyurethane foaming services for foam fill parts. Finally, the parts will be completely finished by adding hardware like hinges, latches, gaskets, lighting, and metal parts to a fully assembled and packaged final product ready to ship to final users.
The outcome of your product can be impacted by the type of powder, the material specifications, the type of mold and even the ambient temperature and humidity. Rotoplast uses state-of-the-art equipment with high-skill employees to ensure consistent results and unbeatable quality.
The rotomolding advantages
Because rotational molding can be done with a variety of material formulations, the process is highly versatile. Here are some advantages of the rotomolding process:
-
Low cost and investment. The low cost for tooling makes small production runs or prototype creation more affordable. As an exemple, a rotational mold can be 10 times less expensive compare to injection molding or blowmolding. Additionally, this process creates less waste material and does not use water in the process.
-
Complicated shapes. Rotational molding can accommodate complex design needs such as stiffening ribs or textured surfaces. The rotomolding process can make complicated shapes with minimal component parts and seams. Therefore, it’s well suited for creating objects used in industries where efficient sanitation is essential.
-
Uniform wall thickness. The rotation enables an even distribution of material to the mold walls, with a heavier quantity settling into the corners. This uniform thickness ensures strong structural integrity. The molded walls can be as thin as 0.125’’ to 0.750’’.
-
Almost no limit to the size. The rotational molding process can be used to produce objects in an incredible range of sizes, from children’s toys to 50,000-litre tanks.
-
Multiple parts can be molded at the same time. The rotomolding machine can accommodate several parts simultaneously. Consequently, a single production run can produce multiple pieces. If a product requires several component parts, the individual parts can be created simultaneously and then assembled to create a single unit.
Best practices and standards for rotomolding processes and materials are established by industry organizations like the British Plastics Federation and the Association of Rotational Molders.
Products manufactured through rotomolding
When it comes to rotomolding applications, the sky is the limit. Here are some common products produced through the rotational molding process:
-
Liquid storage vessels and tanks with capacities up to 50,000 litres
-
Shipping and material handling equipment, such as pallets, crates and insulated containers
-
Sanitation and environmental products, such as septic tanks and water treatment tanks
-
Traffic control equipment, such as road signs, bollards and traffic cones
-
Nautical gear, including docks, watercraft, kayaks, pontoons and buoys
-
Vehicle parts, such as dashboards, air ducks, fenders, roofs and fuel/fluid tanks
-
Powersports accessories, such as cargo box, trunks, seats, bed liners, and covers
-
Playground equipment and park furniture
-
Toys and recreation equipment
-
Lawn and garden products, like planters, watering pitchers and patio furniture
If you have a design idea for a unique tool, toy or decorative object, talk to the Rotoplast team about the possibilities.
FAQ :
What does a rotational molding prototype cost? The cost of a prototype varies according to the part’s size, complexity and material. Because rotational molding can typically be done with molds made of machined or fabricated aluminum, it can be significantly more economical than other production methods.
Who invented rotomolding? Rotational molding was used to create ceramics in ancient Egypt. However, recent history attributes the invention of rotomolding technology to R. Peters, whose 1855 patent described a biaxial rotating mechanism using bevelled gearing and heat to create hollow vessels.
Is 3D printing cheaper than molding? Although 3D printing enables cheap production with minimal material wastage, it can get expensive if production exceeds a small quantity. For medium to large scale production, industrial molding is more economical. Rotomolding can strike the ideal balance of affordability, waste minimization and turnaround time.
What’s the difference between injection molding and rotomolding? The injection molding (IM) process involves melting plastic pellets and then using hydraulic pressure to inject the liquified material into a mold or tool. By contrast, rotomolding involves pouring a powdered substance into the mold, where it’s then heated to its melting point and deposited inside the cavity into the desired form by slow tumbling.