Guide on Plastic Parts Molding Techniques
- Operations PH Media
- Mar 21
- 3 min read
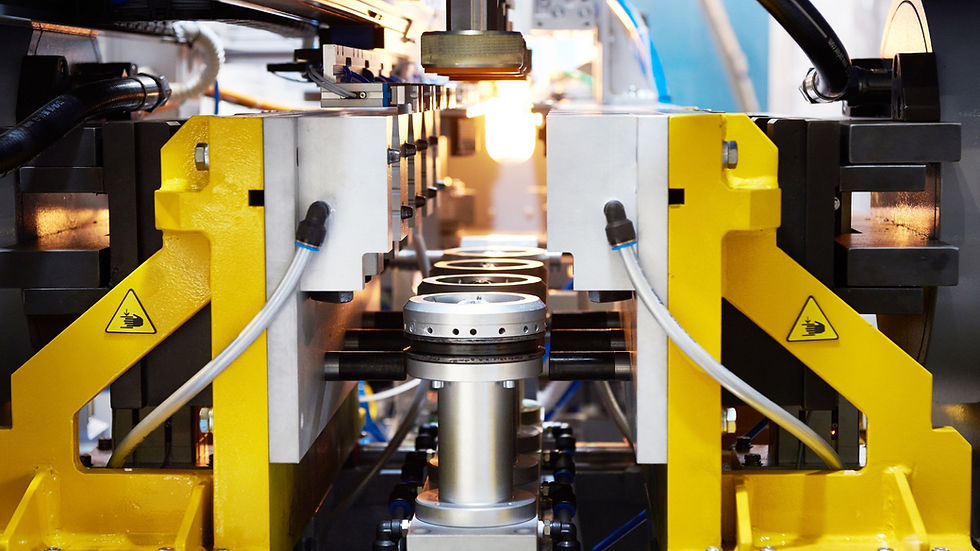
Molding (or molding) plastic parts is at the heart of many industries, from automotive to electronics and consumer goods. Various molding techniques allow us to meet specific needs regarding cost, quality, and production volume. This guide explores the main techniques, their characteristics, costs, and applications to help you choose the method best suited to your project.
Summary Table of Molding Techniques
Technique | Characteristics | Estimated Costs per Technique | Ideal Applications |
Injection Molding | High precision, high volume, high initial cost | $450 – $4,500 | Complex parts in mass production |
Blow Molding | Production of hollow parts (bottles, tanks) | $5,000 – $50,000 | Hollow products, medium to high volumes |
Rotomolding | Large, complex, durable, and resistant hollow parts | $5,000 – $30,000 | Containers, tanks, urban furniture, kayaks |
Compression Molding | Low cost for simple parts, less precise | $1,000 – $20,000 | Small volumes or prototypes |
Extrusion Molding | Continuous long shapes (tubes, profiles) | $30,000 – $250,000 | Continuous products |
Injection Molding
Injection molding is one of the most popular methods for producing plastic parts. The process involves injecting molten plastic under high pressure into a metal mold, typically made of steel or aluminum.
Characteristics
Ideal for complex parts requiring high precision.
Fast cycle time for mass production.
Can use a wide variety of plastics.
Cost
High initial investment
Low cost per part: cost-effective for high volumes.
Applications
Automotive parts (dashboards, bumpers).
Electronic products (phone cases, connectors).
Toys, household utensils.
Blow Molding: For Hollow Parts
Blow molding is a method used to manufacture hollow objects like bottles and tanks. The molten plastic is blown into a mold, where it takes the desired shape.
Characteristics
A quick and efficient technique for producing simple hollow shapes.
Suitable for materials like polyethylene and PET.
Cost
Moderately priced molds: $10,000 to $250,000.
Economical production for medium to high volumes.
Applications
Plastic bottles for beverages.
Industrial containers (tanks, jugs).
Toys (balls, hollow figurines).
Rotomolding
Rotomolding, or rotational molding, is a technique used to produce hollow plastic objects. This process relies on the use of hollow molds and plastic resin powder, which are heated and rotated on two axes to create a uniform part. Rotomolding is particularly appreciated for its ability to create large, durable, and complex objects, without joints or seams.
Characteristics
Ideal for large parts requiring strength and uniformity.
Slower process compared to other techniques.
Low pressure, allowing the use of cheaper molds.
Cost
Moderate production cost.
Economical for low to medium volumes.
Applications
Water tanks, urban furniture (benches, trash cans).
Large toys (play structures).
Agricultural equipment.
Compression Molding
Compression molding is a manufacturing method used to produce plastic or composite parts. This process involves heating a raw material (in powder, pellet, or preform form) and compressing it between two mold halves to give it a specific shape. Once cooled and hardened, the formed part is removed from the mold.
Characteristics
Suitable for small series or prototypes.
Simple technique but less precise.
Compatible with thermosetting plastics.
Cost
Low initial cost: molds typically cost between $1,000 and $10,000.
Ideal for low-volume production.
Applications
Ideal for prototypes.
Small industrial products.
Simple household items.
Extrusion Molding
Extrusion molding, also simply called extrusion, is a molding technique used to produce continuous and uniform shapes from plastics or other thermoplastic materials. This method involves forcing heated material through a die, which determines the final shape of the product.
Characteristics
Quick technique for continuous production.
Limited to simple and linear shapes.
Cost
Moderate investment required.
Highly economical for large-scale production.
Applications
Tubes, pipes, and conduits.
Plastic profiles for windows.
Cable sheathing.
Molds for Plastic Parts by Rotoplast
Rotoplast ensures exceptional precision, durability, and optimal resistance for custom plastic parts. Our goal is to fully meet customer expectations, with active involvement at every stage of the process, from design to mold testing.
Furthermore, Rotoplast offers various types of products and, upon request, a plastic injection molding service. This technique, known for its versatility, allows for high productivity quickly while optimizing production costs. It guarantees robust and high-quality products.
Feel free to contact us for more information or for your custom plastic part molding needs.